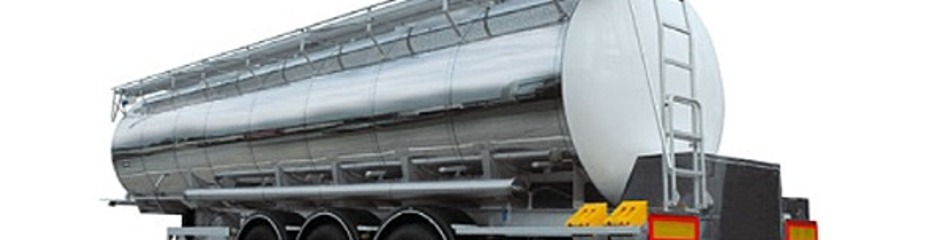
Partnership leads to technical competitiveness
In 1997 the board of the Belgian Van Hool NV, which manufactures buses and indus-trial vehicles, expressed its intention to continue to invest in the production proc-esses and the development of new technologies as well as product ranges in order to support its international expansion. One of these investments was the first Valk Welding welding robot. The two parties then laid the basis for a long-term partner-ship in the area of welding robotisation. "We keep each other sharp by raising the bar together", is how Dani?l Kemp, Manufacturing Manager Commercial Vehicles, explains the partnership.
Investing in the first welding robot placed Van Hool among the early adopters in the area of offline programming. Dani?l Kemp: "That made it possible for us to efficiently weld small series on the robot. At first the operator had to spend more time on programming than on welding. But the evolution of the offline programming system DTPS has now turned that around. Offline programming has turned out to be one of the most important items in the automation process. The company employs one person full time (and 2 to absorb the peaks) for programming in order to keep the 12 robots running flexibly in full produc-tion. But we are now working on automating the programming itself. We will be one of the first in the world to start working with APG (Automatic Path Generator) ourselves, which will take us another step towards further reducing the programming time." APG is a toolkit developed by Valk Welding with open source software that customers can use to create their own specific robot software. APG automatically generates complete programs for the welding robot based on data from CAD and Excel.
Manual welders alongside welding robots
The industrial vehicles department is now using 12 welding robots, the largest three of which are used for chassis building. Despite the move towards automation the company is still employing 300 manual welders. Jos Hendrickx, tank building coordinator: "It is especially difficult to automatically weld stain-less steel tanks owing to the strict require-ments set for leakage prevention." The first systems dating back to 1998 are still being used and we continuously face new automa-tion challenges."
Production in Western Europe
A lot of the work in the market has moved to low wage countries. Dani?l Kemp: "It is only possible to produce competitively in West-ern Europe by automating. A distinguishing feature is that we are able to make top quality products according to customer specifica-tion and in many variants by investing heavily in automation technology. All of our trailers and tankers are therefore custom built, while others make mainly standard products. We will therefore have to continue to invest in production technology, new products and new markets, just as we set out to do in 1998. In that respect I see many similarities with Valk Welding. We entered new markets at the same time, both companies have gone through a strong technological evolution and the organisations have grown sharply as well. That's how we continue to build our futures, both together and individually."