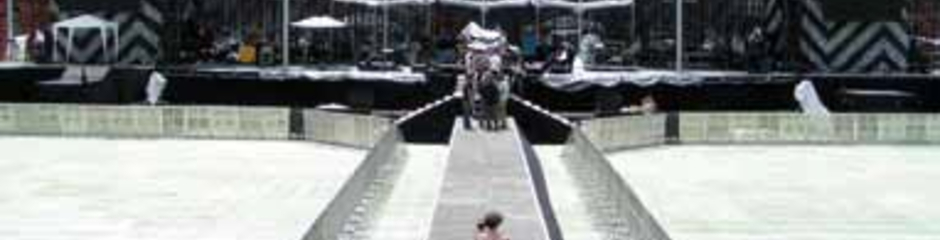
Welding robot cell must speed up production
The products of the Dutch company Mojo Barriers are used all over the world to guarantee the safety of visitors to pop concerts and other major public events. The company name is derived from the most successful product, the Mojo barrier, a modular aluminum segment that can be used to build hundreds of metres of fencing. The Mojo barriers are made by the Dutch supplier Metaal 2000. Metaal 2000 uses a Panasonic welding robot system with the AC Mig welding process for the production of the barriers.
The Mojo barrier has become a household name in the live entertainment industry. The system is used at more than 2000 events a year, all over the world. The first steel version was developed at the end of the eighties, a collapsible element. The barrier has evolved into the current aluminum version over the years. Mojo Barriers is planning to replace all of the steel versions with the new aluminium barriers in the near future.
New aluminum version
Metaal 2000 has been involved since the beginning of the development and product of the barriers. The need for lighter version soon came about for transport and positioning reasons. The material chosen for this purpose was aluminum 50 st/51 st, an alloy with good impact-resistance and high tensile strength. Since this alloy is difficult to place in an edge press, the barriers are assembled by welding together extruded sections, perforated plates and tubular frames.
Large amount of welding
The first 800 aluminum barriers were welded manually. Metaal 2000 employs 14 certified manual welders for this work, all of them able to deliver a high level of quality. The welding of the front sides particular involves a lot of welding. With a large repeat order in the offing, director Jan Kok of Metaal 2000 therefore quickly looked into the possibilities of robot welding for aluminium. He was already using a welding robot cell for steel products. Together with Valk Welding Jan Kok developed a water-cooled jig to minimise the distortion of the material during welding. The jig is a simple design with a clamping system with male-female connectors. Since the clamp and the work piece have a fixed position inserting and removing the products does not call for much professional knowledge. Rather than using the TIG process, Valk Welding recommended the use of AC-Mig welding. That yielded improved annealing and higher quality.
Welding robot cell must speed up production
Valk Welding supplied a welding robot cell with two 3m working stations, which is ample for welding larger parts in the future as well. Metaal 2000 will be using this cell exclusively for welding aluminum products. With the largest order ever on the horizon, both to replace the older steel barriers and to build up the stock, the cell is fully utilised for the time being. Jan Kok expects to be producing the series in a shorter time period in order to leave space for other aluminum welding work.
Water-cooled jig
Unlike the weld quality of the manually welded barriers, Jan Kok regards the consistently high quality provided by the welding robot as a vital factor for the strict quality requirements set for the barriers. A crucial factor here is the use of a water-cooled jig, which makes it possible to keep the application of heat fully under control, which ltimate improves the homogeneity of the weld and keeps the dimensions constant.
AC Mig welding process
Using a welding robot in the fully automatic AC Mig welding process makes it possible to use add much less heat to the end-product in a substantially shorter time period, which reduces the tension in the material and the weld. Once the jig and the welding products have been correctly configured and set (by the Valk Welding product specialists), a product with consistent quality is achieved. Using the fully automatic Mig welding process keeps the amount of melted welding wire the same for each product. This is not the case for the Tig welding process, where the manual feed of the additive depends on the manual welder. The welding quality of the Mig welding process with the welding robot has also contributed substantially to improving the quality of the barriers. , www.metaal2000.n
l