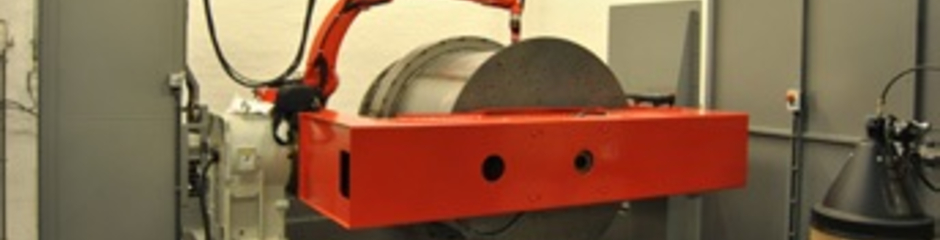
Cimbria’s expertise in welding robots dates back to its foundation more than 25 years ago.
Cimbria’s expertise in welding robots dates back to its foundation more than 25 years ago. The welding robots have specifically been implemented for the welding of silo elements and were partly worn-out and not suitable for offline programming. Niels Ulrik Bliksted, Cimbria Plant Manager states, "We wanted to program our robots offline, so that the product no longer had to be stopped for program-ming, and workpieces can be exchanged between the robots in order to avoid any bottlenecks during the manufacturing. Valk Welding and its Panasonic welding robots, jointly with the DTPS offline program-ming system, was exactly what we were looking for. In the begin-ning we wanted to purchase only one welding robot, but once we had seen all the possibilities, we directly decided to invest in three systems."
Growth through automation
Through automation and a digital order-based manufacturing, Cimbria has nearly doubled its revenue in the past four years. "We aim at a yearly growth of ten percent with the same number of employees. We wish to do this through further auto-mation. The core competence is held in Denmark, while the more labor-intensive production is performed in our factory in the Czech republic," explains Cimbria Plant Manager, Niels Ulrik Bliksted.
Greater flexibility
Last year, the Valk Welding's Danish office installed three welding robots at Cimbria, each oriented at specific components. The largest welding robot system has been installed on a trajectory for the operation of 2 worktables, each with a size of 4.5 m, for the welding manufacturing of silo ele-ments. A second welding robot installation was supplied on an E-frame complete with a drop center on station 1 and a workta-ble with a 4m length on station 2, for the welding of cycle fans.
The third welding robot system processes various products simultaneously. Therefo-re, Valk Welding has provided the welding robot installation with two worktables of 4 m, for the stageless rotation of workpie-ces in the manipulators. This system has the advantage that the operator can take the workpieces in and out at one station, while the robot is welding at the other station.
The welding robot installations are built at the Valk Welding's head office in the Netherlands. For its welding robot instal-lations, Valk Welding applies unique Pana-sonic technology with the integration of a robot control and a welding machine into one unique system (CPU). Components such as robots, controls, manipulators, wire supplies and software are developed and manufactured in-house by Panaso-nic, which allow for the fine-tuning of all mechanisms.
Offline programming
For its offline programming, Valk Welding implements the Panasonic DTPS offline programming system. DTPS has more than four hundred users and is the most used programming system application for Panasonic arc welding robots. DTPS can be seamlessly integrated into 2D and 3D CAD systems, and converts this data directly into programs for the welding robot. The preparation is fully performed on an external PC instead of on a teach pendant on the robot; therefore, the manufacturing at the welding robot is not interrupted. Offline programming offers many more advantages such as 3D simulation, allo-wing for the recognition and prevention of collisions already in the work preparation stage.
Employees following training at EUC
Cimbria uses the new robot centre at EUC Nordvest, where training is provided on Panasonic welding robots. The first employees at Cimbria have already been trained at EUC Nordvest. "We consider it an important advantage that we can send employees for training in offline programming at EUC, where they use the same robots as we do here in the factory," says Niels Ulrik Bliksted. He con-cludes, "A short time ago, we nearly did not use any robots for the manufacturing of silo components. Thanks to our switch to Valk Welding's robots and offline pro-gramming, already 30 percent of all the welding work is performed on the robots. This meets exactly our strategy to achieve growth by means of automation."