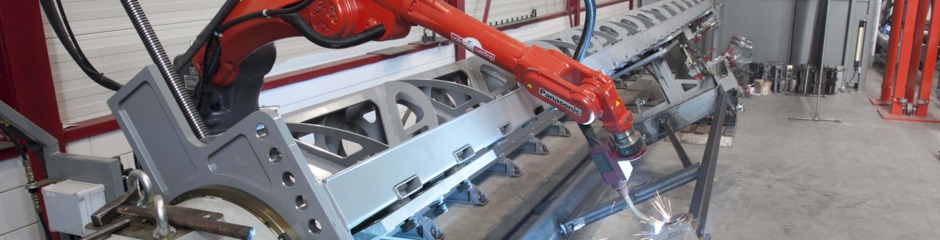
Where manual welders would require three to four hours to weld a complete spray boom, the welding robot at Machine Construction Marknesse gets the same job done in the half the time.
Agrifac Machinery, manufacturers of agricultural crop sprayers, outsourced the production of spray booms for their machines to Machine Structures Marknesse (MCM). Agrifac asked its supplier to improve quality requirements, while also reducing the cost price. MCM found the solution by investing in a welding robot. "It is a big step to start with such a complex product without any prior experience in robot welding. With the support that Valk Welding provided us we got this surprisingly quickly," explained Mark Hilderink, Managing Director.
Doubled
The company has been producing spray booms for Agrifac for many years already. The systems consist of eight booms, which differ in length and height. In recent years annual numbers increased from 600 to 1,500 and it is expected that the numbers will continue to increase. MCM does all of the machining, sheet metal processing and welding work in-house with more than 30 workers and they even established a special department for that purpose. Four fasteners and three manual welders are continuously working on the composition of spray booms. Hilderink and his colleague Einjo Buiskool first had a proper look at the welding robot market before they decided on a robot integrator. "We inspected many references that produce comparable agricultural related structures. Most robot systems are capable of producing high quality welding. The one thing that stood out for us is the offline programming option and what you finally need to correct on the robot in the programme. With the DTPS offline programming system of Valk Welding we could add the programmes one by one on the welding robot."
Stable product uptake
MCM required a robot that could change quickly, that could be used for extensive periods of time, that had a light and flexible product uptake and user-friendly programming. Valk Welding supplied a unit consisting of a Panasonic TA1800 welding robot with the new G3 controller in a longitudinal displacement of 16 meters, two workstations and a DTPS offline programming system. The structure of the product uptake was created by Flevo Engineers and it was made very light and stable. Heavy moulds and spray booms can now be positioned with a relatively light workpiece manipulator. "The cost reduction made a second station feasible, which allows us to load and of low without interrupting production."