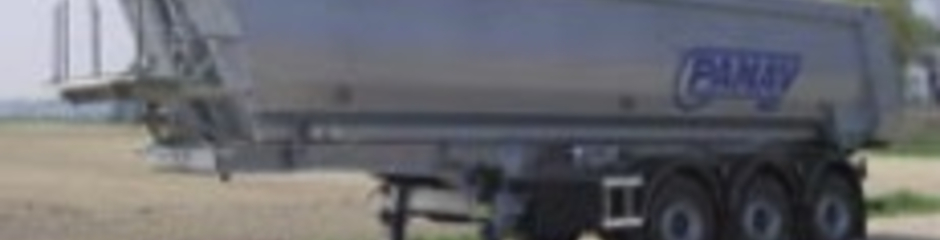
Trailer builder Panav a.s., with its production of 1200 trailers per year and 360 employees, is one of the largest producer of trailers and tippers in the Czech Repu-blic.
Trailer builder Panav a.s., with its production of 1200 trailers per year and 360 employees, is one of the largest producer of trailers and tippers in the Czech Repu-blic. Now that the Czech Republic is making large investments in improvements in infrastructure, Panav is enjoying particular growth in the sales of trailers for heavy transport. However, the required capacity increase cannot be achieved with addi-tional workforce, due to the shortage of skilled professionals in the metal indus-try. This acute problem, which affects the entire Czech region, has been the reason for investing in a welding robot installation supplied by Valk Welding.
Valk Welding CZ, together with Valk Welding engineers in the Netherlands, have developed a welding robot installation for welding chas-sis beams with a length of up to ca 14meters. In order to weld these chassis beams, which consist of three parts, Valk Welding have de-veloped a unique solution, where the welding process is automatically interrupted at the locations of the notches. To achieve this, Valk Welding engineers have incorporated a laser sensor into the trip circuit, which scans the weld to determine its starting and ending points before the welding robot is activated. This system gives rise to huge time savings in the programming phase.
Production increased
According to eng. Ladislav Frycak of Pa-nav, who has supervised the investment in the new welding robot cell, the use of this welding robot is the only way to achieve the required productive increase without deploying additional workforce. The fact that the welding robot also allows savings in staff costs and enables a substantially higher quality of the weld itself, have been impor-tant additional factors in the decision to invest in a welding robot cell of this size. The cell is structured around a Panasonic VR-008L welding robot, which moves along a 22- meter track and can reach the entire length of the chassis beams. The development and construction of the mounting tables on both sides of the track was done in-house by Pa-nav. The positioning of the mounting tables on both sides allows changing the work-piece without interruptions to the welding process. Ladislav Frycak: “The time savings gained through the use of this concept have been so considerable that the preliminary process is now unable to keep up with the welding production on the chassis beams. This means that we are not fully utilising the capacity we now have, but we expect to have reached the point of full utilisation by the end of the year.”
The welding robot cell is only used for welding the chassis beams. The cross-connec-tions and the customer-specific superstructu-res are welded manually. All other operations, such as plasma cutting, composition, irradia-tion, coating and final assembly are done in this order in successive manufacturing areas. For Panav, this welding robot cell is their first experience with welding robots. Neverthe-less, the company had drawn up quite a wish list for the project. The supplier would have to be ISO 9001 certified, and would also be assessed for quality, delivery time, know-how, service and of course price! From ten suppliers, Panav finally chose the proposal submitted by Valk Welding CZ. Valk Welding’s local presence as well as their experience in making long welds for customers including Polish trailer builders Wielton and Belgian bus builders Van Hool, were decisive reasons for the choice they made. The entire cell has been constructed at Valk Welding in the Netherlands, and was built up after testing and acceptance at Panav in January of this year. According to Ladislav Frycak, investing in a cell this size is only profitable at a mini-mum annual production of 1000 trailers (for smaller production volumes, other solutions are certainly possible ed.), so that Panav has the right size for such an investment, and has succeeded in leveraging it to build a position of advantage on the Czech trailer market. The concept of the cell has also taken account of further expansions in robot welding of smal-ler products.
Laser sensor scanning interruption of welding track
The chassis beams for the trailers are con-structed based on a top and bottom plate and a centre piece, with the latter containing notches for cross-connections. To prevent the welding robot from going on welding at the locations of the notches, the welding path is first scanned using a laser sensor which has been integrated into the trip circuit. From a horizontal position, the sensor scans the starting and ending points between two in-terruptions, and then the intervening length of beam is welded. The programmers at Valk Welding have developed a special software-based adjustment to the welding programme to accomplish this. On the part where the sensor does not detect any material (i.e. at the place of the notch), no welding will take place. This also obviates the need for manual preparation of a welding programme consi-sting of 250 to 300 steps, which produces corresponding time savings.
www.panav.cz www.valkwelding.cz