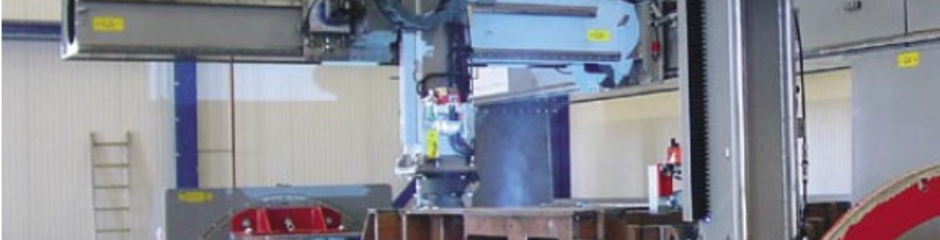
The huge welding robot system that Valk Welding has built for Bollegraaf Recycling Machinery in Appingedam forms part of a sizeable investment programme
The huge welding robot system that Valk Welding has built for Bollegraaf Recycling Machinery in Appingedam forms part of a sizeable investment programme intended to double the production of bale presses within 2 years. Bollegraaf is thus anticipating strong growth in the market for environmental and recycling technology. As well as the welding robot system, the DTPS G2 offline programme system and Valk Welding’s Wire Wizard wire feed system, the investment programme also covers a cutting line and a heavy-duty bending robot. That will make it possible for the company to sharply reduce its lead times and to flexibly produce single articles.
The welding robot system has a longitudinal movement of 33 metres with three transverse movements of 3 metres, combined with a height movement of 1.9 metres. The three Panasonic TA1900-WG welding robots are suspended on the height movement. The work pieces are positioned by 2 manipulators with bearing capacities of 6 and 25 tons. On the heaviest manipulator, complete bale press frames are simultaneously welded by 2 robots. The stamps and large valves for the compression section of the Bollegraaf bale presses are made at the second clamping area. All three robots can work at the same time, and the manipulators can even be steered individually. That means that a total of 27 shafts can be steered separately.
Masterpiece
With the 27 individually steered shafts this project makes full use of the functionalities of the offline programme system DTPS G2. The safety zones are of great importance because the three welding robots must not get in each other’s way. For the head of production, Bram Bos, offline programming was one of the most important preconditions: “We wanted to weld complete frames and also to be able to programme them entirely offline. With that aim in mind our preparations included taking a close look at various shipbuilding and trailer construction projects throughout Europe. Valk Welding was the only robot integrator that had previously delivered such a heavy system, including one to the Polish trailer building Wielton. The decisive factor was the fact that Valk Welding is an organisation with high level technical knowledge of both robotics and welding.”
Action plan
“Getting a project such as this off the ground is by no means an everyday event, either for the supplier or for us. Implementing a system like this involves a completely different working method, which has to be supported by all departments. Also, it was necessary to create the right mindset for programming for single article production. For that reason we created a large project team, comprising 6 people from Bollegraaf and 5 from Valk Welding. That means that R&D, engineering and production people were closely involved in the completion of this project. At the same time a number of employees were trained in programming”, explains Bram Bos.
Sharp reduction in lead times
As well as the benefits of a high repetition precision, business-economic considerations were of great importance to Bollegraaf’s decision to give this automation operation the green light. Bollegraaf’s welders needed a total of 2 weeks (including finishing) to manually weld frames for the bale presses with 3 layer angle welds. The deployment of 2 welding robots reduced the cycle time for a complete frame to 21 hours. Not only has that given Bollegraaf a substantial saving on wage costs, the shorter lead times mean that it is no longer necessary to produce stock parts. That fully meets the objective of raising flexibility and reducing stocks to zero.
Thick plate software
The frames for Bollegraaf’s bale presses are built up with 30mm steel plate. Most of the welding is carried out with angle welds in three layers with 1.2 mm solid SG2 wire in A15 welding height. The use of Thick Plate software makes it possible to automatically build up all layers with a robot program that only traces the first layer, and fast access macros are used to quickly and easily ascertain the tolerance in the product. Bollegraaf Recycling Machinery manufactures products including bale presses for waste paper and systems for processing industrial and domestic waste.