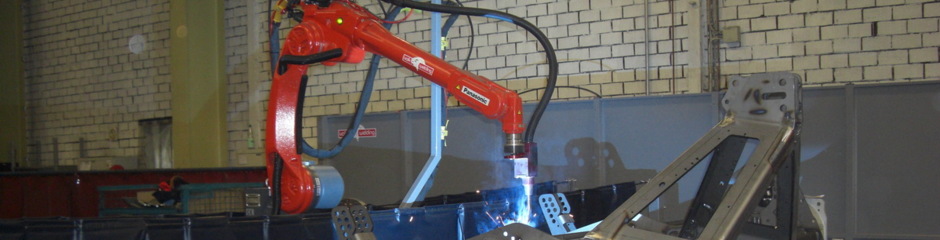
Grimme, located in Damme, Germany, the world leader in agricultural machinery for potato production, has opted for welding robot units from the welding robot specialists, Valk Welding BV.
Grimme has found that the number of product variants continue to increase, while production numbers are reducing; this reduces the options for manual programming using a manual programming unit. Erich Schenkel: "Every new component and any technical change to a pre-programmed product had to be manually programmed on the robot, which meant that the robot was not available for production while programming. This is the reason why management at Grimme had been interested in offline programming for some time already. This provides considerable benefits: increased production capacity due to an uninterrupted production cycle, cycle time calculations, importing of 3D CAD files, 3D simulation with collision detection and recording of welding data."
Panasonic DTPS
DTPS (Desktop Programming and Simulation Software) is specifically designed for arc welding using Panasonic welding robots. Project Engineer Steffen Kahle: "The advantage of offline programming compared with Teach-in is that we can prepare programmes externally without interrupting the welding process. This makes welding of limited product numbers using the robot feasible and it increases the cycle time of the robots."
Equalising tolerances
Components for the Grimme Rotary Hiller (GF) / rotary cutter were initially programmed offline in DTPS. This allowed for components to be directly welded by the robot, without requiring considerable corrections on the part of DTPS. Erich Schenkel: "3D modelling is not automatically displayed in practice. Tolerances can be changed, e.g. while preparing steel sheet components. In order to compare the virtual programme with the actual application we first measure the components with the Quick Touch search system by Valk Welding. Any deviation in the weld is automatically corrected in the programme before the robot starts. The robots therefore provide greater accuracy and a higher quality weld."
Complete design system
Erich Schenkel: "Based on the positive experience and the unique advantages offered by the DTPS system, we commissioned Valk Welding to deliver a robot unit that would be capable of welding the complete design of our Grimme cultivators. Each year we build about 300 Grimme cultivators in different versions. We wanted the unit to have the option to weld all of the different versions (also in the long-term) without requiring additional apparatus. In collaboration with Grimme, Valk Welding developed a solution that facilitates continuous length adjustment of the manipulator counter bearing. The only thing we have to do is select the desired position and DTPS does the rest. When we adjust the weld in the programme, DTPS makes the adjustments for all of the versions. This unique advantage of DTPS was the deciding factor why we decided on the system from Valk Welding."
Basis for the future
Grimme has chosen the Valk Welding system with Panasonic and DTPS as a long-term solution. Erich Schenkel: "There were also other reasons to opt for Panasonic. Panasonic makes welding robots only, i.e. all components, including robots, robot controllers, wire feed motors, manipulators and the programming system all come from one manufacturer. All components are therefore designed to function as a whole. The welding machine and robot controller are integrated with one central processor. Valk Welding specializes in robotic integration in the field of welding automation and it has extensive knowledge and experience in this field."