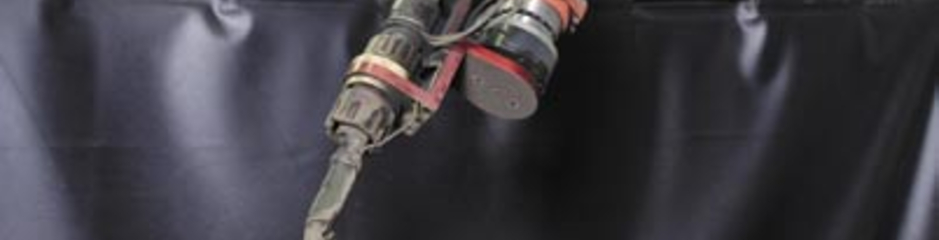
Joskin, which manufactures vehicles for manure spreading and agricultural transport systems, has in recent years invested substantially in increasing its capacity and modernising its welding department.
Joskin, which manufactures vehicles for manure spreading and agricultural transport systems, has in recent years invested substantially in increasing its capacity and modernising its welding department. Seven welding robot systems have now been put into operation at the production facility in Soumagne, close to Luik, and there are more to come. Joskin has thus succeeded not only in sharply raising productivity, but also in achieving a higher and more consistent level of quality. Joskin has opted for the latest welding robot technology of the Panasonic TAWERS welding robots and the DTPS G2 offline programming system.
Employing more than 650 people and with locations in Belgium, France and Poland, Joskin is currently one of Europe’s biggest agricultural vehicle producers. The company’s growth gained momentum as a result of a number of successful products for which Joskin produces all of the parts under its own management. The company has trebled its turnover since opening production facilities in France and Poland.
Initially tired of robots
It will go without saying that a company of this size started using welding robots at an early stage. But Joskin had never succeeded in achieving the desired result with them. Production manager Didier Joskin explains the reasons for that: “The operator was spending more time on programming and optimising the robots than on production. We also had a lot of calibration problems, and were unable to weld a number of products. That led to serious delays in the cycle times, and ultimately resulted in poor productivity levels. Until recently we were pretty tired of robots. We even considered switching to manual welding at our locations in Belgium and Poland.”
Valk Welding convinced
Without much hope, in the summer of 2006 Joskin asked a number of suppliers to make a proposal mainly aimed at achieving a rise in productivity and flexibility and improving the quality of the products for which welding robots were used. Didier Joskin: As a test object, we gave them a hydraulic cylinder, the product we have had the most trouble with. Based on sound preparations, Valk Welding delivered a perfect product and managed to put forward convincing arguments both on the technical front and at company level with its facilities in Alblasserdam. It also became clear that the two companies had more in common than apparent at first glance: a strong family firm character with enthusiastic personnel, a leading market position with a technically cutting edge product and strong growth combined with a healthy outlook. We decided to put the new Valk Welding system into operation as a pilot. After that, everything moved very quickly. The quality was perfect, the productivity rate was 25% to 50% higher, we had no malfunctions, and the setup time turned out to be many times shorter than what we were accustomed to. That prompted our decision to replace all six existing welding robots with Panasonic TAWERS welding robots.”
Hydraulic cylinders
Joskin was experiencing the most problems with the robotised welding of its hydraulic cylinders. The success of this product was therefore an important factor in Joskin’s decision on whether to continue with robot welding. Peter Pittomvils, Valk Welding’s technical consultant: “Joskin makes all of the hydraulic cylinders for its vehicles under its own management. If you look at Joskin’s wide range of products, that will give you an impression of the numbers. That meant that robot welding would have benefits. The main problem was found in welding the nipple on the cylinder. The strong concentration of heat on a small area made it impossible to make the cylinder optimally round. We managed to achieve that on the basis of our expertise and by using the new SP-MAG welding process.”
Standard systems for sub-assemblies
Of the seven welding robots that Valk Welding has supplied to Joskin, the first four are based on an H-frame concept with two clamping tables, a manipulator and high speed doors. Joskin used this relatively simple setup for welding small parts and sub-assemblies. To have a welding robot operate several clamping tables, a fifth cell was fitted with a robot on a longitudinal travel. This setup made it possible to achieve a long activation period for the welding robot. The work pieces were clamped and taken out while the robot was welding at another station. A further two standard cells have recently been added. Didier Joskin: “By using seven cells we’ve succeeded in making more products with one less shift and have fully integrated all of the welding work. This has also given us a guarantee of extra capacity in the future.”
Latest generation of welding robots
For the new welding robot cells, Valk Welding has deployed the latest generation of Panasonic’s TAWERS welding robots. With this robot, which has been purpose built for arc welding, the welding machine and the robot are integrated in a single control system. The extremely high communication speeds that this achieves make the TAWERS the most advanced and fast welding robot on the market. Didier Joskin: “The TAWERS welding robot is a typically advanced top quality Japanese product, with a high level of reliability and which is easy to programme. The welding current source is unique, and facilitates many software functionalities, including a spat-free welding process and integrated welding data registration. The collision detector is especially important to us. In the event of a collision the welding robot switches to soft–servo, which makes the robot arm ‘pliant’, so that no damage can be caused to the torch or robot arm, and does away with the need to recalibrate.”
Offline programming
Offline programming contributes significantly to the productivity gains of the TAWERS welding robots. Valk Welding has been successfully using the programming and simulation system DTPS G2, which it had a hand in developing, for more than ten years. That gives the robot operator control over the entire welding production process, and also makes it possible for him to prepare welding programmes outside of production. That not only yields a higher welding robot activation level, but also facilitates a high level of flexibility. For that reason, it is no
longer the size of the series that determines whether profitable use can be made of welding robots.
Total solution partner
Joskin was aware that outstanding quality and a fault-free supply of welding wire were vital to achieving maximum output. That is why Joskin performed tests - free of obligation - with Valk Welding’s solid welding wire in Ecodrums. Much to Joskin’s surprise, as well as the spat-free end result the wire feed with this welding wire was entirely faultless. The price and production benefits were reason enough for Joskin to switch all of its robots to Valk Welding’s welding wire. Also, with Valk Welding as a “Total Solution Partner”, Joskin only has to deal with a single point of contact. As well as the welding wire, Panasonic welding machines and the company consumables have now been put into operation too.
Complete welding of dumper trucks
Now that Joskin has acquired a taste for robot welding, it has moved on to the welding of larger work pieces. Joskin will be welding complete tipping units for its dumper trucks using the next welding cell, which has now been put together at Valk Welding in Alblasserdam. Didier Joskin: “The technology is already there, as are the internal logistics. The problem is building the right jigs. With this new welding robot cell we plan to welding 6 dumper trucks a day in 1.5 shifts.”
Credit crisis presents new opportunities
By using the new welding robot cells Joskin has succeeded in substantially increasing productivity without employing extra people. Didier Joskin: “Which is just as well, as those extra people are difficult to find in our region. The high production rates have made it possible for us to reduce delivery times. The reduced number of orders caused by the credit crisis is creating more gaps in production and in the organisation. At last we now have time to turn our attention to new markets. We currently have a presence with our products in more than 30 countries, and we are extending our network to Eastern Europe. We are also increasing our marketing efforts to strengthen our position in the countries in which we already operate.”
Continued investment in welding robot technology
Didier Joskin: “Our outlook is good despite the somewhat weaker economic conditions. We plan to continue to invest in welding robots in order to keep pace with the anticipated growth in turnover. We will soon be delivering our 24,000th tank and the 7,000th dumper truck.