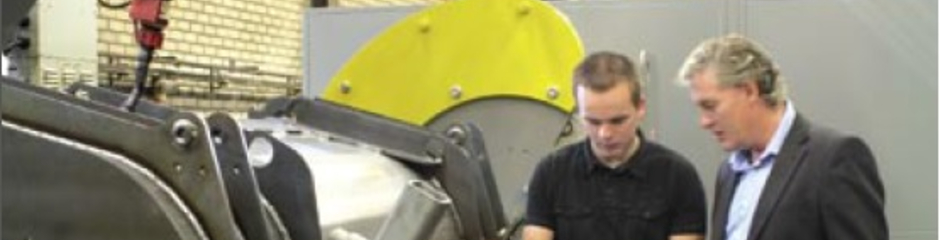
The practical approach of Valk Welding and the functionalities offered by the programming system DPTS G2 persuaded father and sons Kampert of Hekamp Werktuigen en Aanbouwdelen to purchase a new welding robot system from Valk Welding.
The practical approach of Valk Welding and the functionalities offered by the programming system DPTS G2 persuaded father and sons Kampert of Hekamp Werktuigen en Aanbouwdelen to purchase a new welding robot system from Valk Welding. At the beginning of this year Valk Welding delivered a robot unit and programming system for the welding production of complete shovelling and loading buckets for the agricultural and excavation sectors. Marco Kampert: “Our experiences with an existing welding robot that no longer had enough capacity for our current production level made us more open to a practical approach than to glib sales arguments. Valk Welding not only delivered the system, but also continued to support us afterwards until the final 10% was solved.”
Driving through the farming area in Kootwijkerbroek, the last thing people would expect to see is an ultra-modern production company. This is where in the nineteenfifties Henk Kampert Sr. began to manufacture shovelling and loading buckets for the local farming sector. That activity has since developed into a modern family firm producing machinery and accessories with some 800 customers in the Netherlands, Belgium, Germany and Denmark and a production level of around 4000 products a year.
Ample capacity with 4 clamping units
Hekamp contacted Valk Welding to ask whether it was possible to have its large products weighing more than 1000 kg welded with a robot and to programme the entire system offline. To facilitate maximum flexibility and sufficient capacity for large products and separate parts alike, Valk Welding proposed a solution with 4 clamping units, operated by 1 mounted welding robot. The system ultimately delivered by Valk Welding comprises a Panasonic TAWERS TA 1900 WG welding robot on an 18.5 metre freely programmable track that can be used on 4 clamping units. The first 2 stations are for heavy products and are therefore equipped with 3000 kg manipulators and a moment of up to 10,000 n/m. The third station has a clamping unit with a 1000 kg manipulator. A fourth station is intended for small sub-assemblies, and is therefore fitted with a preliminary turntable. The four clamping units make it possible to weld series and varied single items with the robot without having to keep changing the clamping jigs.
Completely produced in-house
The products are manufactured and coated completely in-house with a lead time of about 3 weeks. Most of them are variants of standard products which differ between clients in terms of length, width, height and mounting. For this purpose Hekamp has its own plasma cutting system, a forming and welding department and a powder coating department. For each order the items are delivered as a construction pack to the welding department, where Hekamp personnel compile the orders and provisionally attach them to an external station.
Final welding with the robot
Completely assembled and provisionally attached buckets often weighing hundreds of kilos are transported from the external stations to the welding robot. A bucket weighing 500 kg, for instance, is completely welded by the welding robot with an A6 welding height in about two hours. Marco Kampert: “Despite the fact that you can programme much more accurately with DTPS than online, you have to bear in mind that the actual model is always a bit different from the 3D simulated product.” That’s why for the final welding of this type of rough product, the starting position of the weld is located by means of tactile searching. A welding seam monitoring system is then used during the welding procedure. That way, minor differences in pre-opening and positioning are perfectly welded shut. That makes it possible to use offline programming without correction.
DTPS easy to learn
All of the products are designed and detailed in Solidworks. Article lists are then generated for the cutting of the flat parts. Solidworks files can be imported directly in DTPS to create the welding programs for the robot. Marco Kampert: “In the initial stage, a program had to be written for the welding robot for all the products. We programmed the first products together with Alex Hol of Valk Welding, and after that we were soon able to continue on our own. We’ve now pretty much got the hang of the programme, and it’s also possible to copy many existing cycles from an existing programme and paste them into a new one.”
Combination enhances flexibility
Marco Kampert: “All in all the system with 4 work stations and external programming have helped us to achieve a high degree of flexibility. Whereas the previous system was programmed online and was only costeffective for series work, we can now make several products in small series. That means that we can limit the stocks we keep and weld more products with the robot without having to keep changing the jigs. External programming is an important element of this as it makes it possible for you to visualise the entire scenario of product, jig and
robot and simulate the whole welding cycle. You can also plan production on that basis. With the support of Alex Hol, we quickly got the hang of the system. But it came as a complete surprise that we were able to use the system so soon.”