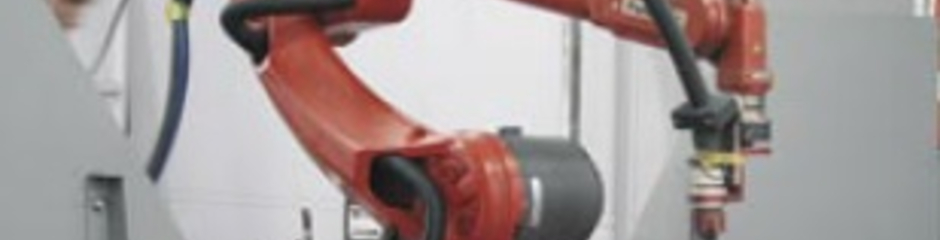
When the Belgian wheelchair manu-facturer Vermeiren set up an operation in Southern Poland in 1994 under the name of Reha-Pol-A , two Panaso-nic welding robots supplied by Valk Welding moved to Poland as well.
When the Belgian wheelchair manu-facturer Vermeiren set up an operation in Southern Poland in 1994 under the name of Reha-Pol-A , two Panaso-nic welding robots supplied by Valk Welding moved to Poland as well. This was Valk Welding’s first customer on the Eastern European market. Meanw-hile, the 15 welding robot installations supplied by Valk Welding to Reha-Pol-A have produced an enduring customer-supplier relationship. Reha-Pol-A is a classic example of a company with high-volume production according to strict quality standards, which delivers 80,000 wheelchairs per year from Poland to the entire global market. This makes Reha-Pol-A the largest producer of wheelchairs in Europe.
The deployment of welding robots at Reha Pol-A was actually not inspired primarily by labour cost savings, which is an impor-tant issue in Western Europe, but purely by efficiency considerations. The 15 welding robot cells ensure a daily output of 250 pcs in 3-shift operation, something which manual welding simply cannot compete with. Another important factor is the reliably high weld quality of this type of product. The production facility in Poland was expanded in 2004 by 10,000 sq m; it is now used to construct only the frames for the more than forty different types of designs.
The base material for all types is 2 mm thin-walled piping material, which is punched, bent and laser-cut. The tools Reha-Pol-A employs to achieve this include modern BLM bending machines and an Adige tube laser. All these components have to be welded together to form complete frames. The welding robot cells which Valk Welding has supplied to Reha-Pol-A for this purpose are all based on the H-frame concept, with two revolving mounting tables of 3 m per cell. The advantage of this design is that welding always takes place at a single mounting table, which enables optimal running times for the welding robot. The dimension of 3 m was chosen to have sufficient mounting space to weld all components for a given type on a single cell. Each cell has been fitted to accommodate 1 or 2 types. For that reason, the oldest types are still being robot-welded using the original Panasonic welding robots of the AW generation, which were installed in the late 1980s. Meanwhile, these welding robots are nearly twenty years old and have run over 50,000 production hours. As long as the old wheelchair models are still on the market, we are making efforts to keep these welding robot cells in operation.
General Manager Slawomir Golec was in-volved in the deployment of welding robots from the earliest beginnings. He sees nothing but benefits in the cooperation and support offered by Valk Welding. “The know-how available to Valk Welding in this area is simply not to be found in Poland at this time. Our people have now learned enough to be able to solve maintenance and malfunction-re-lated issues independently. With the local presence of Valk Welding (Reha-Pol-A is only a two-hour drive from Ostrava), we are bene-fiting from shorter communication lines and having support in our own language.”
For the future, Slawomir Golec counts with an increase in labour costs, which are cur-rently still low in European terms. They are the main determinant of the cost of the assembly process. “Manual craftsmanship will always remain important. Therefore, you need to make continuous improvements in efficiency, especially in frame production. We try to achieve that by continually using the latest available technologies, among other things. Therefore, the latest robot cells include the latest Panasonic TAWERS welding robots.” The General Manager specifically mentions the high velocity of the new gene-ration of robots, their collision detection and the splash-free welding process as the main strengths. Collision detection is a software-based solution which shuts the welding robot down immediately in case of excessive loads on the torch and trip circuit. The advantage is that the operator can switch the welding robot back on without the need for recali-bration, which produces considerable time savings.