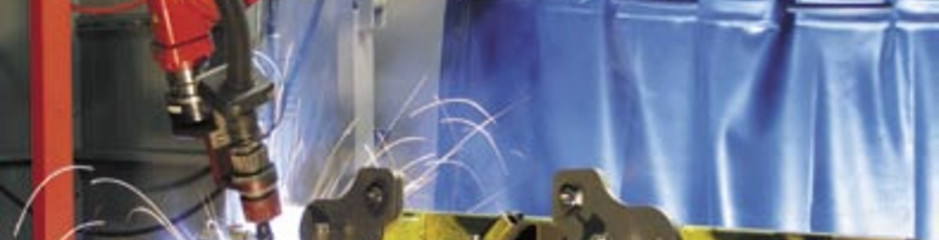
Thule Towing Systems, owner of Brink Trekhaken, wants to automate its production process further - it plans to leave the product insert in the welding-robot installations to handling robots.
Thule Towing Systems, owner of Brink Trekhaken, wants to automate its production process further - it plans to leave the product insert in the welding-robot installations to handling robots. This should not only produce savings on Thule’s wage costs, it should also eliminate the need to make a separate jig for each type of towing hook. The manufacturer has started a pilot project with Valk Welding that is set to serve as an example for all the welding-robot installations of the Thule Group in the Netherlands and France.
Currently, Thule Towing Systems uses fifteen welding-robot installations in its production site in Staphorst, where loose components are welded into complete towing hooks. In 1990, Valk Welding supplied to first cell with a Panasonic welding robot of the AW genera-tion, which is still used in a two-shift system in 2007. All the welding-robot installations that were supplied subsequently are built on the basis of the H-frame concept, always with the latest generation of Panasonic wel-ding robot. With this concept, the company was far ahead of its time. The robot com-pletely welds the towing hook on one side, whilst the operator places the loose compo-nents in the jig for the next towing hook on the other clamping table.
Thule Towing Systems would like to take that process a step further. Purchasing Manager Wim Feddes and the responsible Manufac-turing Engineer, Jojanneke Krabbe, explain why. “We have a separate jig for each type of towing hook, and that makes a total of 2,000 jigs. Producing a jig costs a lot of time and the components need to fit exactly. If they do not fit exactly or if the jig is damaged, the robot welding process is disrupted, and the welding robot stops.” “For each towing hook, the operator needs to insert an average of five components in the jig. That is monotonous manual work for which you could use a handling robot. Hand-ling robots are able to place the loose com-ponents one by one in the correct position against each other, after which the welding robot can tack and weld them. You can com-pose a towing hook component by compo-nent without using a jig. This requires more programming work, but you can programme and simulate it all offline.”
Currently, the people of Thule Towing Sy-stems are analysing with Valk Welding how you can set up the feed and discharge of the components and the completed towing hook, how you establish the correct position of the loose components and how you deal with tolerance differences. Valk Welding is developing software-based solutions, and the project group of Thule Towing Systems is exploring the opportunities offered by Vision systems.
Within the Thule Group they strive towards standardisation in order to have the option to exchange production parts with other sites. Wim Feddes, “That also means we strive towards one supplier for welding robots and welding wire. We believe that Valk Welding has the best track record; they have an enormous know-how and they have the drive to turn this project into a success. They also have a welding and a handling division that work closely together. On one of the trade fairs, Valk Welding showed a pilot setup for a jigless welding cell, where a handling robot and a welding robot welded a product together. It should be clear by now that this is a learning and development process for Valk Welding too, but they have gained our confidence.”