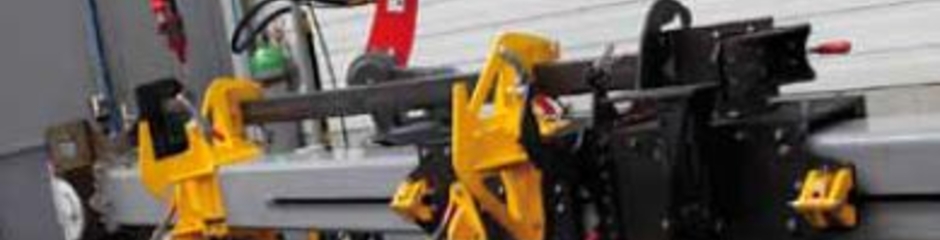
Mass production of small series
If you as company want to supply a top quality product and give the customer value for money, the production and organisation have to be perfectly matching to each other. Profielnorm in Zeeland's Tholen succeeds in this by continu-ously investing, which makes it possible for them to stand out in the world of mezzanines. The company has recently in-vested substantially in automation and the certification of its welding production. The company is now able to weld small series with a minimum retooling time using the automatic software developed by Valk Welding for the welding robot. Profielnorm is now able to automatically weld a large volume of varied products. A successful project, made possible by Valk Welding's hardware and software solution and the joint development of the welding jig.
With its mezzanines Profielnorm offers smart and affordable solutions for space problems in the building sector and industry. With its modular system of cold-shaped girders and trusses and welded columns the company is able to supply a tailor-made structure for any project. The columns have to be given head and foot plates, and have different connec-tions and measurements. In each project this means that a large number of variants of a similar product have to be programmed and clamped. Until recently Profielnorm was using an OTC welding robot, which had to be programmed separately for each col-umn. Engineer Peter Flikweert: ”Despite the advantage of copy and paste for separate software blocks, the programming took up a lot of time. Also, the robot did not have a weld seam tracking system and the accuracy declined with time, which made it necessary to reprogram. The robot was simply due for replacement."
Need for easy programming
By purchasing a new welding robot system Profielnorm was looking to take automation a step further. Jos Schot, managing director of Profielnorm: “We wanted our operators to be able to quickly select a programme without first having to go through configuration and adjustment steps. It takes a robot integra-tor with in-depth knowledge of software to achieve that. In our search for a suitable sup-plier we found that Valk Welding is well ahead of the crowd. After seeing a few examples of completed projects we had every confidence in them. Based on their DTPS programming system Valk Welding has in recent years de-veloped a number of software building blocks that can be used to automate the program-ming of similar products. A unique aspect is that we are able to devote our own specific welding know-how to this and then adapt the data to it ourselves afterwards.
Automatic Path Generator
APG (Automatic Path Generator) for DTPS is a toolkit developed by Valk Welding with open source software that customers can use to create their own specific robot software. APG automatically generates complete programmes for the welding robot, which - in addition to the positioning of the welding torch - contain the right torch angle and the right welding parameters, such as amperage, voltage, weaving parameters, crater filling pa-rameters, etc. APG works like CMRS (Custom Made Robot Software) as a DTPS plug-in.
Stratified software structure
Paul van den Bos, teamleader of Valk Weld-ing's software department: "We have opted for a stratified software structure composed of the modules CMRS, APG, DTPS and the robot software. With that aim in mind we've laid down the welding programs for all connec-tions in a DTPS database. On the input side we've created a simple CMRS input screen in which the operator enters the type of column, shoring, base and head plate, which column length is required and which quantities are to be welded. The selected column connection is also displayed in graph form so that the opera-tor can check that it's the right model straight away. Once the information has been entered APG retrieves the necessary base programs from the DTPS database and automatically gener-ates the welding path for the welding robot."
Two stations
To ensure that the robot is able to continue welding while the columns are loaded or taken out, the system is equipped with two working stations of respectively 4.5 and 7.5 m which are served by a Panasonic TA 1900 welding robot on a 12-metre track. The welding robot is equipped with a Valk Welding robot torch with a pneumatic safety holder, which ensures that the robot immediate stops if there is a crash and that the welding torch is not deformed. A Wire Wizard wire guidance system has been installed between the weld-ing wire drum and the robot to ensure that the wire is fed smoothly and without any friction.
Jointly developed welding jig
Profielnorm developed the jig in close consul-tation with Valk Welding and then built it itself. Engineer Peter Flikweert: ”We wanted to be able to clamp four columns next to each other and have them attached and welded by the robot. Valk Welding checked in DTPS whether the welding robot could get to all required positions. At first, that was not the case. After looking at various alternatives we eventually created at a carousel, which provides sufficient accessibility for 4 columns. The jig consists of top, end and support sections that we can adjust along the whole length. The jig was made for the maximum column measurement of 160 x 160 mm and we use filler blocks for smaller sizes. The advantage of four columns per station is that the welding time for each station is a bit longer so that the operator doesn't have to walk backwards and forwards between the stations as often."
NEN 1090 certified
Profielnorm is among the first group of com-panies certified for the new NEN 1090 and the accompanying ISO standard (NEN 1090-2 and ISO 3834), which has been required for construction parts since July 1st 2014. The specifications for this were written by an International Welding Technologist (IWT). Managing director Jos Schot: "In our mission we set out to stay close to our customers with our systems and to project an image of quality and reliability. This certification makes us well-fit and well-organized for the market. In that respect I see similarities with the organisation of Valk Welding. “In the meantime the first 4.5 m station has been fully optimised and we are copying it entirely to the 7.5 m station. There is still enough space for a second, identical cell at a later stage.